Ảnh hưởng của quá trình gia công
Khả năng đạt được một dung sai hoặc bề mặt nhất định nào đó là một chức năng của quá trình gia công. Phần này mô tả các khả năng chung của các quy trình khác nhau về dung sai và độ nhám bề mặt và tính toàn vẹn bề mặt (tính nhất quán/ tính đồng nhất).
Các phương pháp gia công
Một số quy trình gia công vốn đã chính xác hơn những quy trình khác. Hầu hết các quy trình gia công khá chính xác, có khả năng đạt dung sai ±0.05 mm (±0.002 in) hoặc nhỏ hơn. Ngược lại, sản phẩm đúc bằng khuôn cát thường không chính xác, và có dung sai lớn gấp 10 đến 20 lần so với sản phẩm sử dụng bằng các phương pháp gia công khác được chỉ định. Bảng 5.4 liệt kê một loạt các quy trình gia công và chỉ ra dung sai điển hình cho từng quy trình.
BẢNG 5.4: Giới hạn dung sai điển hình, được dựa trên khả năng xử lý bởi các quy trình gia công khác nhau. | |||
Quy trình | Dung sai điển hình, mm (in) | Quy trình | Dung sai điển hình, mm (in) |
*Đúc cát: | *Mài nhám: | ||
Gang | ±1.3 (±0.050) | Mài bóng | ±0.008 (±0.0003) |
Thép | ±1.5 (±0.060) | Chà nhám | ±0.005 (±0.0002) |
Nhôm | ±0.5 (±0.020) | Mài giũa | ±0.005 (±0.0002) |
Đúc chết
(Đúc áp lực) |
±0.12 (±0.005) | *Không thuộc truyền thống và nhiệt: | |
*Đúc khuôn nhựa: | Gia công hóa học | ±0.08 (±0.003) | |
Polyethylene | ±0.3 (±0.010) | Phóng điện | ±0.025 (±0.001) |
Polystyrene | ±0.15 (±0.006) | Điện hóa. mài | ±0.025 (±0.001) |
*Gia công: | Điện hóa. máy móc | ±0.05 (±0.002) | |
Khoan
6mm (0.25in) |
±0.08±0.03
(+0.003/-0.001) |
Cắt tia lửa điện | ±0.08 (±0.003) |
Phay | ±0.08 (±0.003) | Cắt tia laze | ±0.08 (±0.003) |
Tiện | ±0.05 (±0.002) | Cắt hồ quang plasma | ±1.3 (±0.050) |
Dung sai dựa trên khả năng xử lý của hoạt động gia công cụ thể. Dung sai cần được chỉ định là một tính năng của kích thước chi tiết; chi tiết lớn hơn đòi hỏi miền dung sai lớn hơn. Bảng liệt kê dung sai cho các chi tiết có kích thước vừa phải trong mỗi phương thức gia công chế tạo. Quá trình gia công quyết định đến bề mặt hoàn thiện và tính toàn vẹn bề mặt. Một số quy trình có khả năng tạo ra chất lượng bề mặt tốt hơn so với những quy trình khác. Nói chung, chi phí gia công xử lý tăng lên đồng thời với sự cải tiến chất lượng bề mặt hoàn thiện. Điều này là do các hoạt động bổ sung và thường tiêu hao nhiều thời gian hơn để có được bề mặt chất lượng ngày càng tốt hơn. Các quy trình được ghi nhận để cung cấp các yếu tố chất lượng hoàn thiện vượt trội cho bề mặt chi tiết bao gồm mài giũa, chà nhám, đánh bóng và gia công siêu mịn. Bảng 5.5 chỉ ra độ nhám bề mặt thông dụng được dự tính từ các quy trình gia công khác nhau.
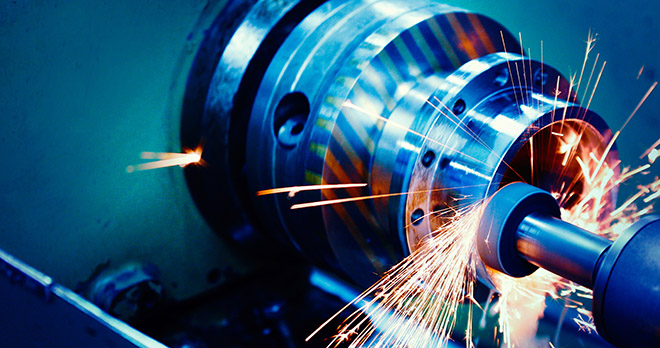
Gia công tiện
BẢNG 5.5 Giá trị độ nhám bề mặt được tạo bởi các quy trình gia công khác nhau. | ||
Quy trình | Hoàn thành kết quả điển hình | Phạm vi độ nhám |
*Đúc: | ||
Đúc chết (Đúc áp lực) | Tốt | 1–2 (30–65) |
Đúc mẫu chảy (Đúc mẫu sáp) | Tốt | 1.5–3 (50–100) |
Đúc cát | Kém | 12–25 (500–1000) |
*Tạo hình kim loại: | ||
Cán nguội | Tốt | 1–3 (25–125) |
Dập kim loại tấm | Tốt | 1–3 (25–125) |
Ép lạnh | Tốt | 1–4 (30–150) |
Cán nóng | Kém | 12–25 (500–1000) |
*Gia công: | 0.5–6 (15–250) | |
Doa | Tốt | |
Khoan | Trung bình | 1.5–6 (60–250) |
Phay | Tốt | 1–6 (30–250) |
Khoét | Tốt | 1–3 (30–125) |
Chép hình, theo vết, bao hình | Trung bình | 1.5–12 (60–500) |
Cưa | Kém | 3–25 (100–1000) |
Tiện | Tốt | 0.5–6 (15–250) |
*Mài nhám: | ||
Mài bóng | Rất tốt | 0.1–2 (5–75) |
Mài giũa | Rất tốt | 0.1–1 (4–30) |
Chà nhám | Rất rất rốt | 0.05–0.5 (2–15) |
Đánh bóng | Rất rất rốt | 0.1–0.5 (5–15) |
Mài siêu tinh | Rất rất rốt | 0.02–0.3 (1–10) |
*Không thuộc truyền thống | ||
Phay hóa học | Trung bình | 1.5–5 (50–200) |
Điện hóa | Tốt | 0.2–2 (10–100) |
Phóng điện | Trung bình | 1.5–15 (50–500) |
Cắt tia lửa điện | Trung bình | 1.5–15 (50–500) |
Cắt tia laze | Trung bình | 1.5–15 (50–500) |
*Nhiệt: | ||
Hàn hồ quang | Kém | 5–25 (250–1000) |
Cắt tia lửa | Kém | 12–25 (500–1000) |
Cắt hồ quang plasma | Kém | 12–25 (500–1000) |