Công nghệ in 3D kim loại ra đời trên thế giới và hiện nay nó liên tục phát triển, ở Việt Nam hiện tại công nghệ này còn rất mới và chưa được phát triển nhiều, một số công ty lớn có sử dụng in 3D kim loại thì cũng chỉ là nhập máy từ nước ngoài về để phục vụ việc sản xuất. In 3D vật liệu kim loại là một mảng lớn yêu cầu chi phí đầu tư và công nghệ nhiều hơn các mảng khác trong lĩnh vực in 3D
Trong phần giới thiệu về in 3D kim loại này, chúng tôi đề cập đến các nguyên tắc cơ bản của SLM và DMLS. Sau khi đọc bài viết này, bạn sẽ hiểu các cơ chế cơ bản của SLM và DMLS và những lợi ích cũng như hạn chế của công nghệ in 3d kim loại hiện nay
1/ Sự khác biệt SLM & DMLS là gì?
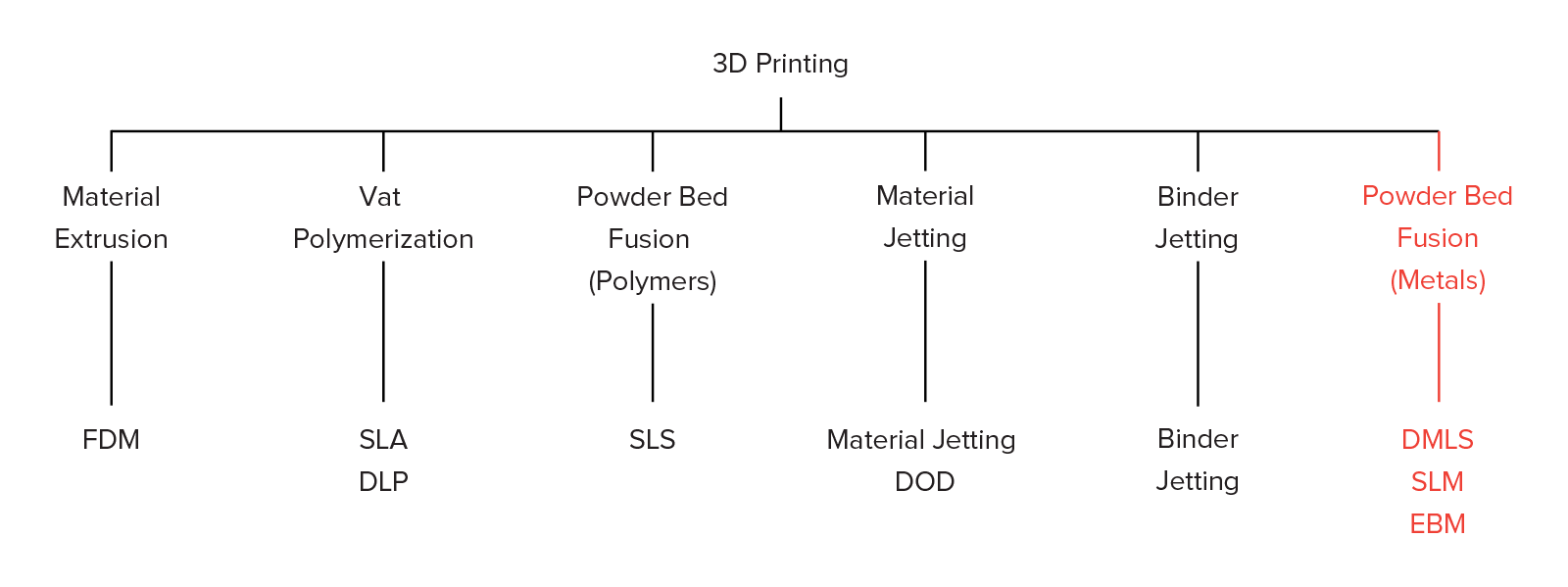
Laser thiêu kết nóng chảy (SLM) và thiêu kết kim loại trực tiếp (DMLS) là hai quy trình sản xuất bù đắp kim loại thuộc về công nghệ in 3D hợp nhất giường bột. Hai công nghệ này có rất nhiều điểm tương đồng: cả hai đều sử dụng tia laser để quét và hợp nhất có chọn lọc (hoặc làm tan chảy) các hạt bột kim loại, liên kết chúng lại với nhau và tạo thành từng lớp chồng lên nhau. Ngoài ra, các vật liệu được sử dụng trong cả hai quá trình là kim loại ở dạng hạt.
Sự khác biệt giữa SLM và DMLS thuộc về các nguyên tắc cơ bản của quá trình liên kết hạt (và cả bằng sáng chế): SLM sử dụng bột kim loại với nhiệt độ nóng chảy duy nhất và làm tan chảy hoàn toàn các hạt, trong khi trong DMLS, bột được tạo thành từ các vật liệu có điểm nóng chảy thay đổi cấp độ phân tử ở nhiệt độ cao.
Bản chất: SLM sản xuất các bộ phận từ một kim loại duy nhất , trong khi DMLS sản xuất các bộ phận từ hợp kim kim loại
Cả SLM và DMLS đều được sử dụng trong các ứng dụng công nghiệp để tạo ra các sản phẩm kỹ thuật sử dụng đầu cuối ( sử dụng được ngay) . Trong bài viết này, chúng tôi sử dụng thuật ngữ In 3D kim loại để chỉ cả hai quy trình nói chung và chúng tôi mô tả các cơ chế cơ bản của quy trình chế tạo cần thiết cho các kỹ sư và nhà thiết kế để hiểu những lợi ích và hạn chế của công nghệ.
Có các quy trình sản xuất bù đắp khác có thể được sử dụng để sản xuất các chi tiết kim loại khối đặc, chẳng hạn như Electron Beam Melting (EBM) và Siêu âm (UAM). Tính khả dụng và ứng dụng của chúng bị hạn chế, vì vậy chúng sẽ không được trình bày ở đây. Nhấn vào đây để biết thêm thông tin về Binder Jinder kim loại .
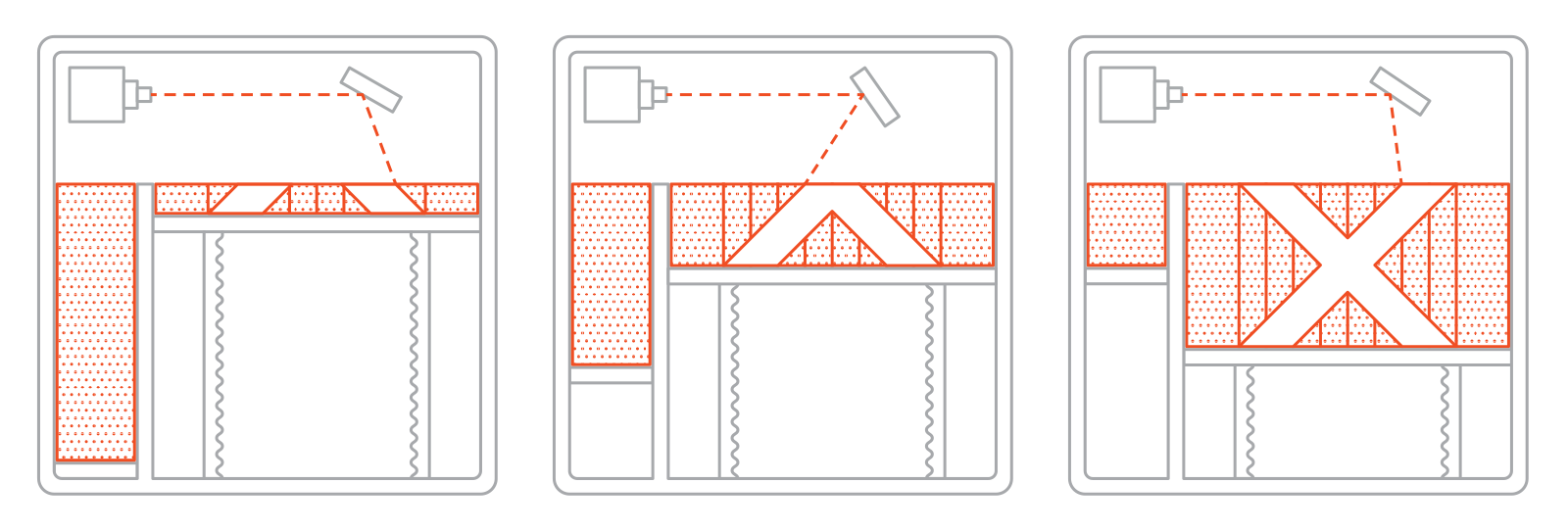
2/ Metal 3D Printing ( IN 3D kim loại) hoạt động như thế nào?
Quy trình chế tạo cơ bản cho SLM và DMLS rất giống nhau. Đây là cách nó làm việc:
- Buồng tạo hình trước tiên chứa đầy khí trơ (ví dụ argon) để giảm thiểu quá trình oxy hóa của bột kim loại và sau đó nó được nung nóng đến nhiệt độ tạo hình tối ưu.
- Một lớp bột kim loại mỏng được trải trên bàn in và tia laser công suất cao quét mặt cắt ngang của chi tiết, làm tan chảy (hoặc nung chảy) các hạt kim loại lại với nhau và tạo ra lớp tiếp theo. Toàn bộ khu vực của mô hình được quét, do đó chi tiết được tạo hình hoàn toàn vững chắc.
- Khi quá trình quét hoàn tất, bàn in di chuyển xuống dưới theo độ dày một layer và lớp phủ sẽ trải một lớp bột kim loại mỏng khác. Quá trình được lặp lại cho đến khi toàn bộ chi tiết được hoàn thành.
Khi quá trình tạo hình kết thúc, các sản phẩm in sẽ lẫn trong bột kim loại. Không giống như quá trình tổng hợp bột polymer (như SLS), các bộ phận được gắn vào bàn in thông qua các cấu trúc hỗ trợ. Phần support in 3D kim loại được tạo hình bằng vật liệu tương tự như chi tiết in và luôn được yêu cầu để giảm thiểu sự cong vênh và biến dạng có thể xảy ra do nhiệt độ xử lý cao.
Khi thùng nguội đến nhiệt độ phòng, bột thừa được loại bỏ bằng tay và các sản phẩm thường được xử lý nhiệt trong khi vẫn được gắn vào bàn in để giảm bớt mọi ứng suất dư. Sau đó, các sản phẩm được lấy ra khỏi tấm in bằng cách cắt, gia công hoặc dây EDM và sẵn sàng để sử dụng hoặc xử lý nguội thêm sau đó
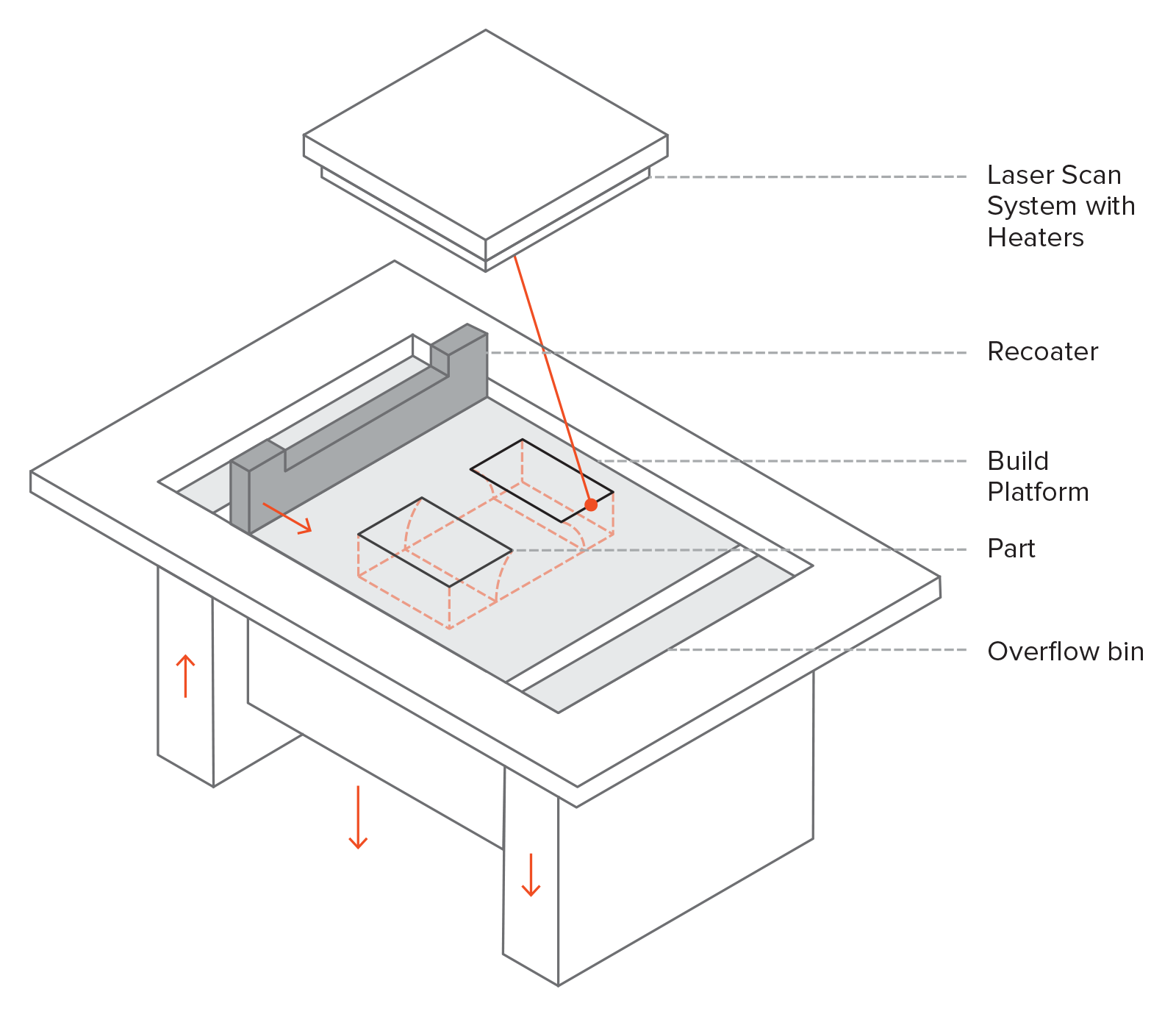
3/ Đặc điểm của SLM & DMLS
3.1/ Thông số máy in 3D kim loại
Trong SLM và DMLS, hầu hết các tham số quy trình được cài đặt bởi nhà sản xuất máy in 3D. Các chiều cao lớp sử dụng trong in 3D bằng kim loại dao động từ 20 đến 50 micron và phụ thuộc vào các tính chất của bột kim loại (độ linh động, phân bố kích thước hạt, hình vv).
Kích thước in điển hình của hệ thống in 3D kim loại là 250 x 150 x 150 mm, nhưng cũng có sẵn các máy lớn hơn (lên tới 500 x 280 x 360 mm). Độ chính xác về kích thước mà máy in 3D kim loại có thể đạt được là xấp xỉ ± 0,1 mm.
Máy in 3d kim loại có thể được sử dụng để sản xuất hàng loạt nhỏ, nhưng khả năng của hệ thống in 3D kim loại giống với khả năng sản xuất hàng loạt của máy FDM hoặc SLA hơn so với máy in SLS: chúng bị hạn chế bởi khu vực in có sẵn (hướng XY), vì các bộ phận phải được gắn vào bàn in.
Bột kim loại trong SLM và DMLS có khả năng tái chế cao: thường dưới 5% bị lãng phí (bỏ đi). Sau mỗi lần in, bột không sử dụng được thu thập, sàng và sau đó được phủ lên trên bằng vật liệu nguyên bản đến mức cần thiết cho lần chế tạo tiếp theo.
Lãng phí trong in kim loại mặc dù ở dạng cấu trúc support, rất quan trọng cho việc tạo hình thành công nhưng có thể làm tăng đáng kể số lượng vật liệu cần thiết (và chi phí).
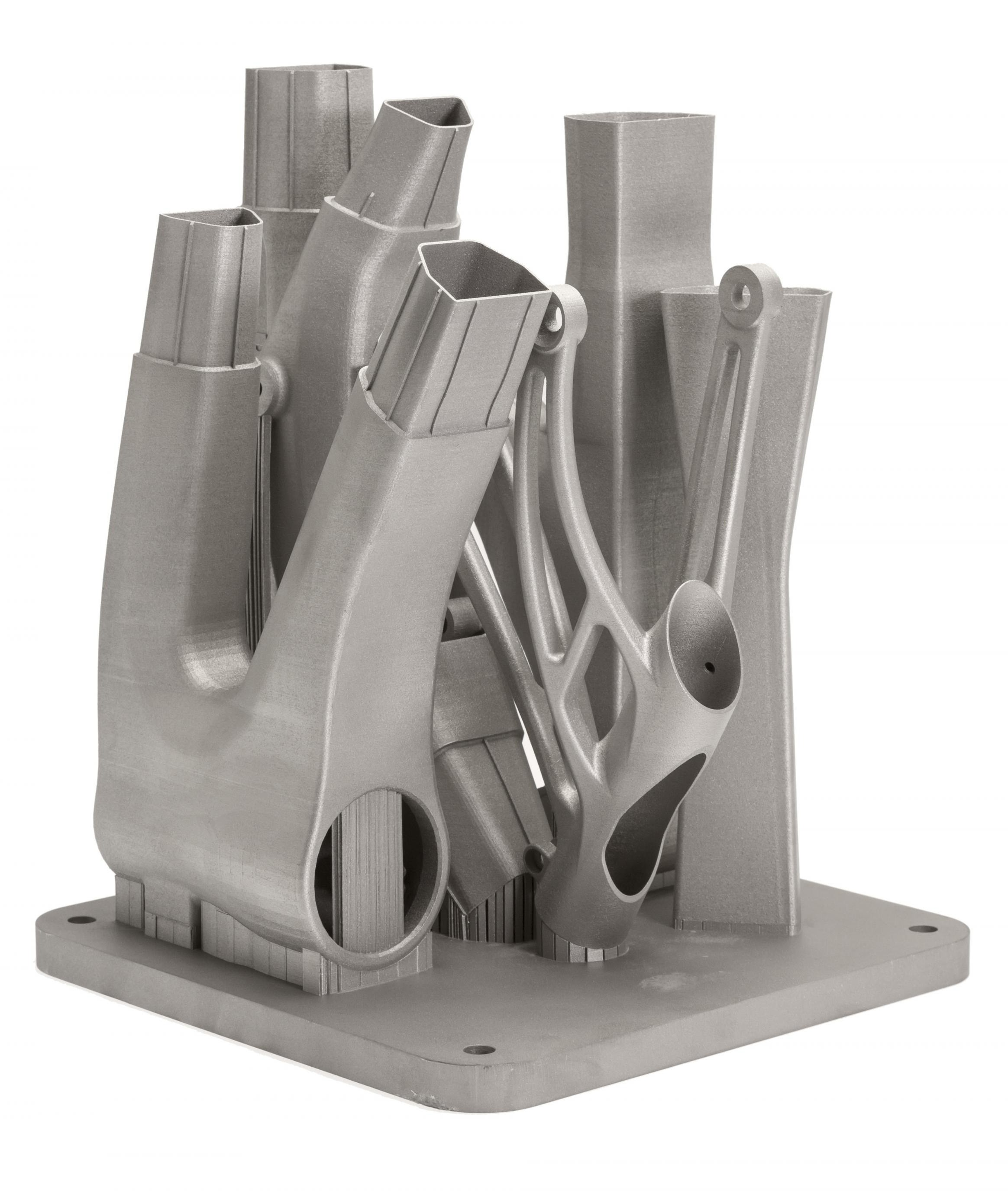
3.2/ Lớp dính
Các chi tiết SLM và DMLS kim loại có các tính chất cơ học và nhiệt gần như đẳng hướng . Chúng rắn chắc với độ xốp bên trong rất ít (dưới 0,2 – 0,5% ở trạng thái được in và gần như biến mất sau khi xử lý nhiệt).
Các chi tiết in 3d kim loại có độ bền và độ cứng cao hơn và thường linh hoạt hơn các chi tiết được sản xuất bằng phương pháp truyền thống. Tuy nhiên, chúng dễ bị nứt gãy.
Ví dụ: hãy xem các tính chất cơ học của hợp kim in 3D kim loại AlSi10Mg EOS và hợp kim đúc A360 . Hai vật liệu này có thành phần hóa học rất giống nhau, chứa nhiều silicon và magiê. Các bộ phận in có tính chất cơ học vượt trội và độ cứng cao hơn so với vật liệu rèn.
Do dạng hạt của vật liệu chưa được xử lý, độ nhám bề mặt được xây dựng (Ra) của phần in 3D bằng kim loại là khoảng 6 – 10 μm. Độ nhám bề mặt tương đối cao này có thể giải thích một phần độ bền mỏi thấp hơn .
AlSi10Mg (hợp kim in 3D) | A360 (Hợp kim đúc) | |
---|---|---|
Sức mạnh năng suất (chủng 0,2%) * | XY: 230 MPa Z: 230 MPa | 165 MPa |
Sức căng * | XY: 345 MPa Z: 350 MPa | 317 MPa |
Mô-đun * | XY: 70 GPa Z: 60 GPa | 71 GPa |
Độ giãn dài khi nghỉ * | XY: 12% Z: 11% | 3,5% |
Độ cứng ** | 119 HBW | 75 HBW |
Độ bền ** | 97 MPa | 124 MPa |
Lưu ý:
*: Xử lý nhiệt: ủ ở 300oC trong 2 giờ
**: Đã thử nghiệm trên các mẫu được tạo hình
3.3/ Cấu trúc support & gá đặt chi tiết
Các cấu trúc support luôn được yêu cầu trong in kim loại, do nhiệt độ xử lý rất cao và chúng thường được chế tạo bằng cách sử dụng mô hình mạng tinh thể.
Hỗ trợ in 3D kim loại phục vụ 3 chức năng khác nhau:
- Họ cung cấp một bàn in phù hợp cho lớp tiếp theo được xây dựng.
- Chúng giữ chi tiết vào tấm bàn và ngăn ngừa cong vênh .
- Chúng hoạt động như một bộ tản nhiệt tản nhiệt ra khỏi chi tiết và cho phép nó làm mát ở tốc độ được kiểm soát nhiều hơn.
Các chi tiết in 3d kim loại thường được định hướng ở một góc để giảm thiểu khả năng cong vênh và tối đa hóa sức mạnh của chi tiết theo các hướng quan trọng. Tuy nhiên, điều này sẽ làm tăng số lượng hỗ trợ cần thiết, thời gian xây dựng, chất thải vật liệu và (cuối cùng) tổng chi phí.
Độ cong vênh cũng có thể được giảm thiểu bằng cách sử dụng các mẫu quét ngẫu nhiên . Chiến lược quét này ngăn ngừa sự tích tụ của các ứng suất dư theo bất kỳ hướng cụ thể nào và sẽ thêm một kết cấu bề mặt đặc trưng cho bộ phận.
Do chi phí in kim loại rất cao, mô phỏng thường được sử dụng để dự đoán hành vi của bộ phận trong quá trình xử lý. Các thuật toán tối ưu hóa cấu trúc liên kết cũng được sử dụng không chỉ để tối đa hóa hiệu suất cơ học và tạo ra các bộ phận nhẹ mà còn để giảm thiểu sự cần thiết của cấu trúc hỗ trợ và khả năng cong vênh.
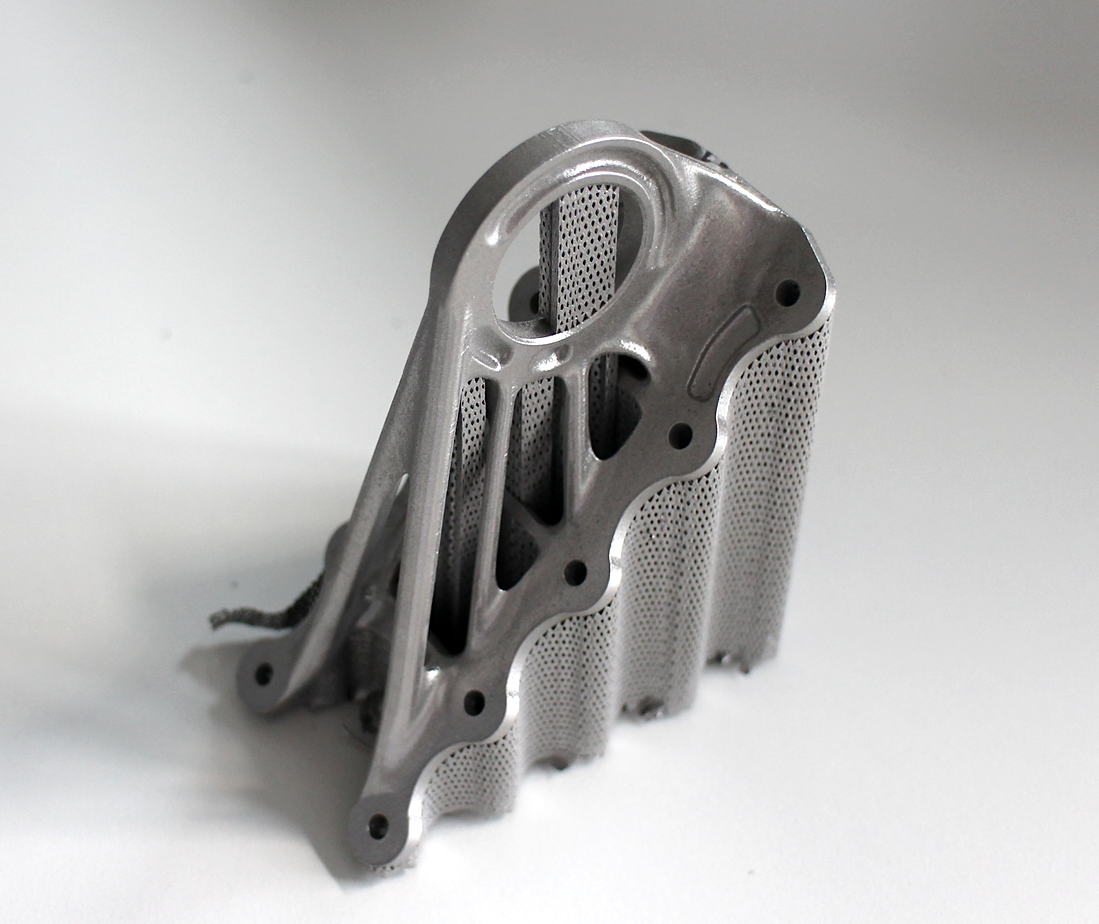
3.4/ Phần rỗng & cấu trúc nhẹ
Không giống như các quy trình tổng hợp bột polymer như SLS, các phần rỗng lớn không được sử dụng phổ biến trong in kim loại vì các cấu trúc hỗ trợ (support) có thể dễ dàng được gỡ bỏ.
Đối với các kênh dẫn bên trong lớn hơn 8 mm, nên sử dụng mặt cắt kim cương hoặc hình giọt nước thay vì hình tròn, vì chúng không yêu cầu cấu trúc hỗ trợ. Hướng dẫn thiết kế khác về SLM & DMLS có thể được tìm thấy trong các tài liệu in 3d .
Thay thế cho các phần rỗng, các chi tiết có thể được thiết kế với vỏ và lõi. Vỏ và lõi được xử lý bằng cách sử dụng năng lượng laser và tốc độ quét khác nhau, dẫn đến tính chất vật liệu khác nhau. Sử dụng vỏ và lõi rất hữu ích khi sản xuất các chi tiết có tiết diện lớn, vì chúng làm giảm đáng kể thời gian in và khả năng cong vênh và sản xuất các bộ phận có độ ổn định cao và chất lượng bề mặt tuyệt vời.
Sử dụng cấu trúc mạng tinh thể cũng là một chiến lược phổ biến trong in 3D kim loại để giảm trọng lượng của một bộ phận. Các thuật toán tối ưu hóa cấu trúc liên kết cũng có thể hỗ trợ trong việc thiết kế dạng trọng lượng nhẹ hữu cơ .
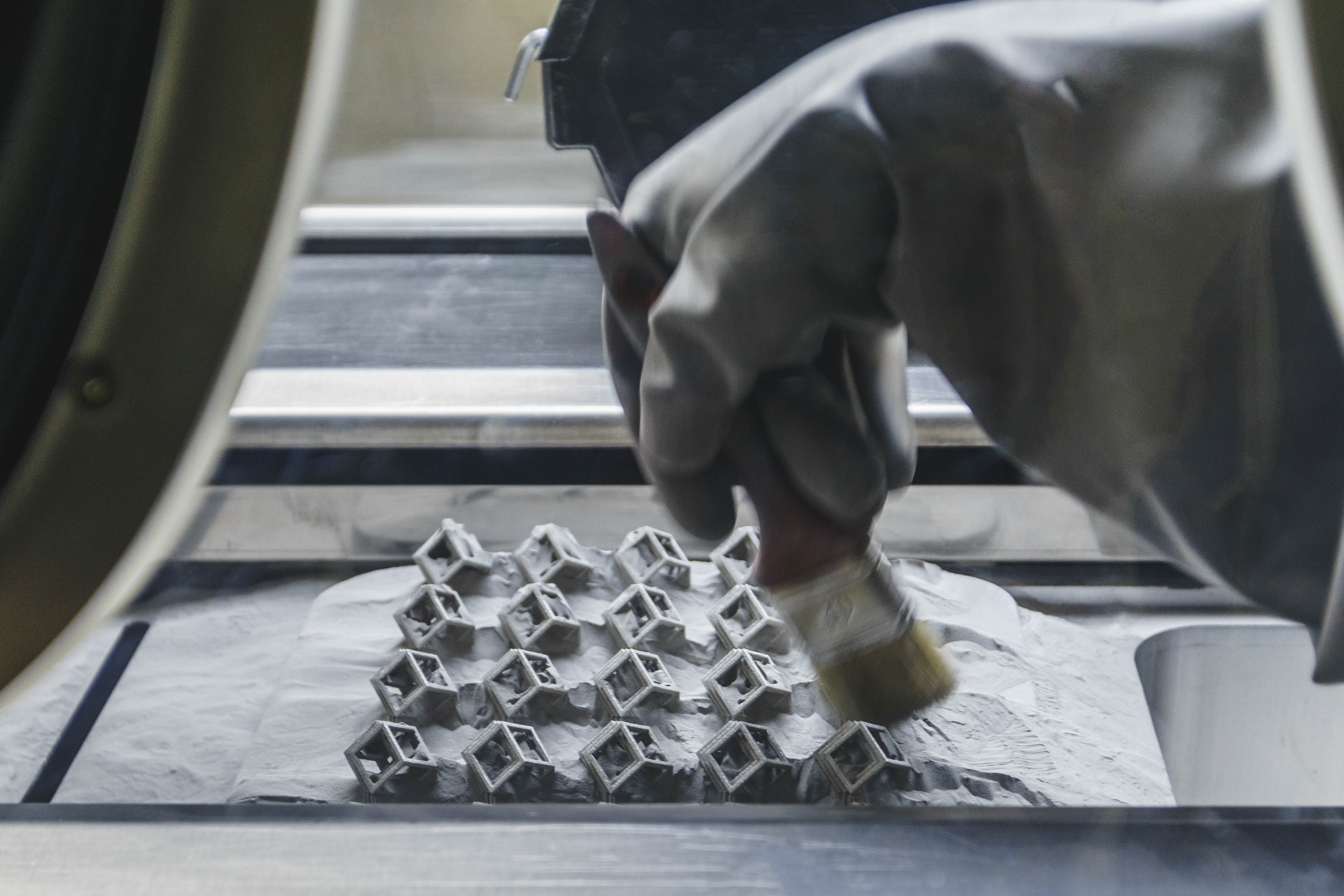
4/ Vật liệu in 3d kim loại SLM & DMLS
in 3D kim loại SLM và DMLS có thể sản xuất các bộ phận từ một lượng lớn kim loại và hợp kim kim loại bao gồm nhôm, thép không gỉ, titan, crôm coban và inconel. Những vật liệu này đáp ứng nhu cầu của hầu hết các ứng dụng công nghiệp, từ hàng không vũ trụ đến y tế. Kim loại quý, chẳng hạn như vàng, bạch kim, palađi và bạc cũng có thể được xử lý, nhưng các ứng dụng của chúng là rìa và chủ yếu giới hạn trong chế tạo đồ trang sức.
Giá thành của bột kim loại rất cao. Ví dụ, một kg bột thép không gỉ 316L có giá khoảng $ 350 – $ 450. Vì lý do này, giảm thiểu khối lượng chi tiết in 3d và hạn chế việc thêm hỗ trợ (support) là chìa khóa để giữ chi phí càng thấp càng tốt.
Một thế mạnh quan trọng của in 3D kim loại là khả năng tương thích với các vật liệu cường độ cao, chẳng hạn như siêu hợp kim niken hoặc coban-crôm, rất khó xử lý với các phương pháp sản xuất truyền thống. Tiết kiệm chi phí và thời gian đáng kể có thể được thực hiện, bằng cách sử dụng in 3D kim loại để tạo ra một phần hình gần lưới mà sau đó có thể được xử lý sau để hoàn thiện bề mặt rất cao.
Vật chất | |
---|---|
Hợp kim nhôm |
|
Thép không gỉ và thép công cụ |
|
Hợp kim titan |
|
Siêu hợp kim Cobalt-Chrome |
|
Siêu hợp kim niken (Inconel) |
|
Kim loại quý |
|
5/ Xử lý nguội
Các kỹ thuật xử lý nguội khác nhau được sử dụng để cải thiện các tính chất cơ học, độ chính xác và sự xuất hiện của các bộ phận in kim loại.
Các bước xử lý sau bắt buộc bao gồm loại bỏ bột lỏng và các cấu trúc hỗ trợ, trong khi xử lý nhiệt (ủ nhiệt) thường được sử dụng để làm giảm các ứng suất dư và cải thiện tính chất cơ học của bộ phận.
Gia công CNC có thể được sử dụng cho các tính năng quan trọng về chiều (như lỗ hoặc ren). Nổ phương tiện, mạ kim loại, đánh bóng và gia công vi mô có thể cải thiện chất lượng bề mặt và độ bền mỏi của một phần in kim loại.
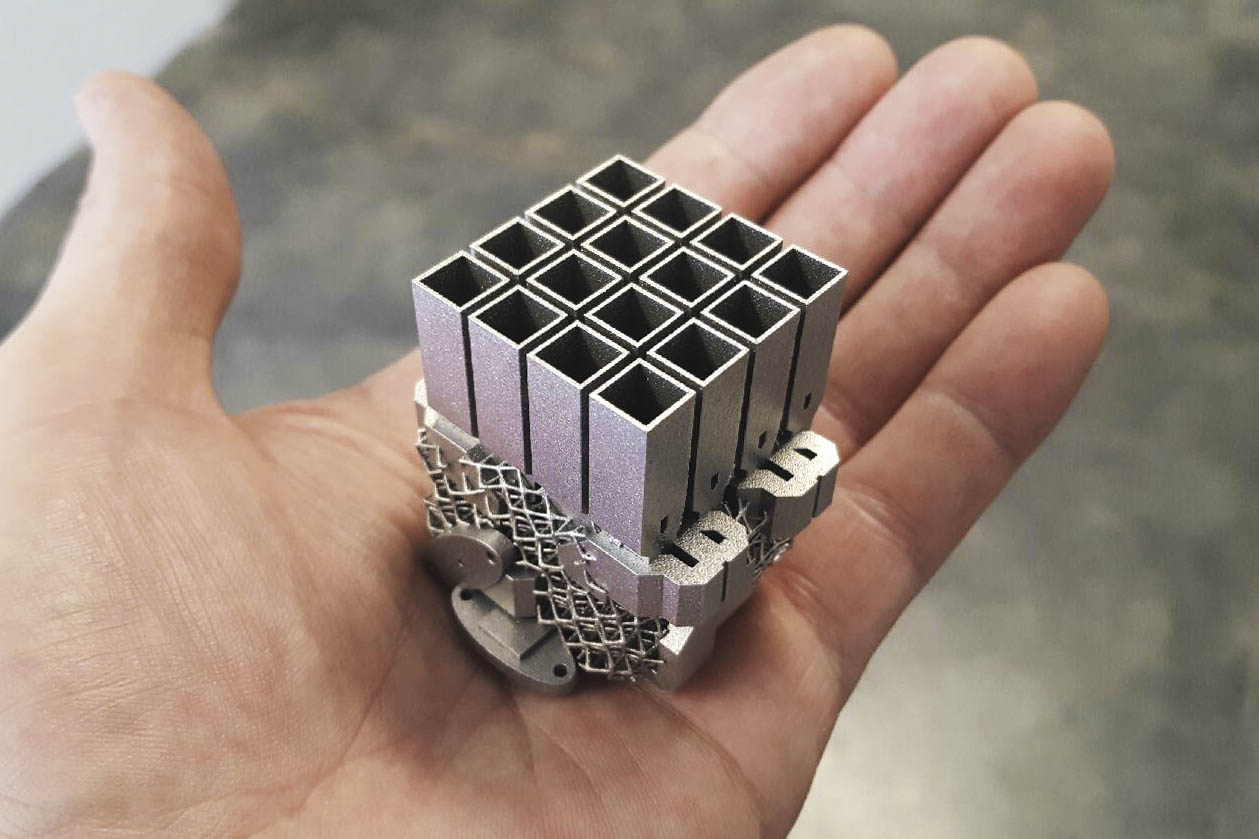
6/ Lợi ích và hạn chế của in 3D kim loại
Dưới đây là những ưu điểm và nhược điểm chính của quy trình in 3D kim loại:
- Các quy trình in 3D kim loại có thể được sử dụng để sản xuất các bộ phận phức tạp, riêng biệt với hình học mà phương pháp sản xuất truyền thống không thể sản xuất.
- Các bộ phận được in 3D bằng kim loại có thể được tối ưu hóa theo cấu trúc liên kết để tối đa hóa hiệu suất của chúng trong khi giảm thiểu trọng lượng của chúng và tổng số thành phần trong một cụm.
- Các bộ phận in 3D kim loại có các tính chất vật lý tuyệt vời và phạm vi vật liệu có sẵn bao gồm khó xử lý các vật liệu khác, chẳng hạn như siêu kim loại.
- Chi phí vật liệu và sản xuất kết nối với in 3D kim loại cao, vì vậy những công nghệ này không phù hợp với các bộ phận có thể dễ dàng sản xuất bằng phương pháp truyền thống.
- Kích thước xây dựng của các hệ thống in 3D kim loại bị hạn chế, vì điều kiện sản xuất chính xác và kiểm soát quy trình là bắt buộc.
- Các thiết kế đã có sẵn có thể không phù hợp cho in 3D kim loại và có thể cần phải thay đổi.
Hướng dẫn thiết kế chi tiết mẫu in 3D kim loại được đưa ra trong bài viết này của Cơ sở Kiến thức. Các đặc điểm chính của hệ thống SLM và DMLS được tóm tắt trong bảng dưới đây:
In 3D kim loại (SLM / DMLS) | |
---|---|
Nguyên vật liệu | Kim loại & hợp kim kim loại (nhôm, thép, titan, v.v.) |
Độ chính xác kích thước | ± 0,1 mm |
Kích thước khổ in điển hình | 250 x 150 x 150 mm (tối đa 500 x 280 x 360 mm) |
Độ dày lớp phổ biến | 20 – 50 mm |
Support | Luôn luôn cần thiết |
7/ Kinh nghiệm
- In 3D kim loại là phù hợp nhất cho các bộ phận phức tạp, tùy chỉnh khó khăn hoặc rất tốn kém để sản xuất với các phương pháp truyền thống.
- Giảm thiểu nhu cầu về cấu trúc hỗ trợ sẽ giúp giảm đáng kể chi phí in kim loại.
- Tối ưu hóa cấu trúc là rất cần thiết để tối đa hóa lợi ích bổ sung của việc sử dụng in kim loại.
- Các bộ phận in 3D bằng kim loại có các tính chất cơ học tuyệt vời và có thể được sản xuất từ nhiều loại vật liệu kỹ thuật, bao gồm cả siêu kim loại.
Nguồn: https://www.3dhubs.com/knowledge-base/introduction-metal-3d-printing
Xin chào, tôi có thể giới thiệu máy in 3D kim loại của chúng tôi với bạn để xem liệu hai công ty chúng ta có thể làm việc với nhau được không?